di Michele Cifalinò
ll sistema di gestione di Salute, Sicurezza ed Ambiente (nel seguito HSE) è costituito da una struttura organizzativa che permette di prevedere, prevenire ed affrontare le varie e complesse situazioni che sorgono dalle interazioni fra l’attività produttiva dell’uomo e l’ambiente.
Un sistema HSE tiene conto anche delle attività attinenti la produzione, le sostanze utilizzate, i prodotti, i servizi, le risorse umane ed organizzative operanti in azienda e delle relative interconnessioni esistenti, in particolare con il Sistema di gestione della qualità.
Le norme di riferimento sono ISO 9001 (sistema di gestione della qualità), ISO 14001 (sistema di gestione dell’ambiente) e ISO 45001 (sistema di gestione della sicurezza sul lavoro). Questi tre sistemi di fatto nascono come indipendenti gli uni dagli altri, ma la fusione in un’unica prospettiva permette di gestire al meglio il processo produttivo d’impresa, grazie a una visione d’insieme delle peculiarità di ciascun sistema ISO. Vediamo più da vicino come funziona un sistema di gestione integrato della sicurezza per l’industria di processo.
La gestione integrata nell’industria di processo
Per garantire che la produzione sia sicura e conforme alle normative, occorre prima di tutto comprendere perfettamente il processo e i rischi a esso associati: conducendo attenti studi sulla sicurezza di un processo chimico non solo si impedisce il verificarsi di reazioni incontrollate, ma si evita anche che gli impianti vengano danneggiati o distrutti e che le persone subiscano lesioni, oltre a tutelare l’ambiente dall’inquinamento.
L’obiettivo delle valutazioni relative alla sicurezza è ottenere una panoramica di tutti i potenziali pericoli, con effetti e conseguenze: vengono coperti aspetti come la sicurezza dei processi e dei prodotti, quella personale e la tutela ambientale. La sicurezza da un certo punto di vista è un tema che rientra anche nella fase di progettazione vera e propria del processo produttivo, che possiamo vedere in diverse fasi.
- Diagramma di flusso a blocchi del processo, che mostra tutte le principali fasi del processo.
- Condizioni operative di processo e specifiche dei materiali impiegati (materie prime, catalizzatori, solventi, coadiuvanti tecnologici, materiali di imballaggio e così via)
- Bilanci materiali ed energetici (reazioni chimiche coinvolte, bilanci energetici ecc…)
- Identificazione dei rischi per l’incolumità dei lavoratori e per l’ambiente;
- Attuazione di strumenti per la programmazione, il controllo, il monitoraggio, l’esecuzione di
verifiche ispettive.
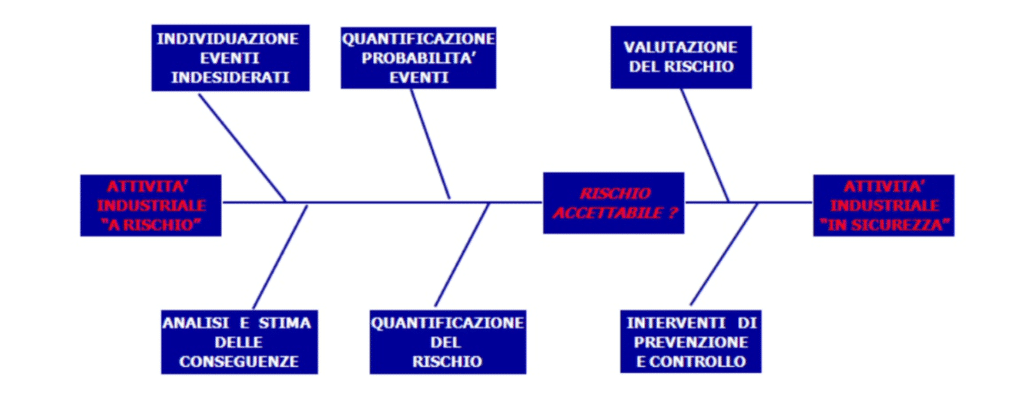
Come mostra la figura, grande attenzione è riservata alla valutazione dei rischi: le conseguenze di incidenti o problemi che possono verificarsi negli stabilimenti chimici spaziano da problemi di lieve entità, che comportano la perdita di un lotto o lievi danni all’impianto, a situazioni disastrose, con lesioni o decesso dei dipendenti, impianti gravemente danneggiati o addirittura distrutti, danni ambientali e nei casi più gravi vittime in un’ampia zona nei dintorni dell’impianto. L’analisi di rischio si può applicare a qualsiasi aspetto e in qualsiasi momento ovvero ad un campo variegato di pericoli e di scenari collegati che possono generare eventi accidentali indesiderati.
La fase di “preparazione” deve essere molto accurata per cicoscrivere lo studio e definirne l’obiettivo, selezionare il personale e le competenze utili per svolgere lo studio e raccogliere tutte le informazioni necessarie. I passaggi che si applicano nell’ottica di una valutazione integrata del rischio sono:
- Identificare i pericoli: individuare le sostanze chimiche pericolose, considerando i prodotti, sottoprodotti, flussi di riciclaggio, spurgo, nonché scarichi pianificati nelle fognature, nell’atmosfera, nelle discariche, nei riciclatori.
- Stimare il potenziale di perdita: a seconda della tipologia di scenario è opportuno valutare tutte le possibili conseguenze legate ai rischi di incidente nell’impianto.
- Stimare la probabilità di avere un incidente: a seconda della frequenza stimata di un certo guasto o incidente è possibile avere un’idea dell’impatto economico e ambientale.
- Identificare i principali rischi
- Valutazione di strategie di intervento o progetti intrinsecamente più sicuri
Il primo passo importante è individuare sul piano qualitativo tutti i pericoli relativi al contesto oggetto di studio e tutti gli scenari potenzialmente pericolosi che possono configurarsi: per ogni sostanza ad esempio, determinare se è pericolosa e in caso affermativo, il grado di pericolo che presenta. Bisogna considerare la salute, l’infiammabilità, l’instabilità e i rischi speciali: per questo aspetto è fondamentale tra l’altro utilizzare un’etichettatura efficiente.
Il secondo passaggio è valutare gli effetti fisici conseguenti ad eventi accidentali e quantificare le conseguenze di danno ipotizzabili. Segue la quantificazione degli eventi che si avvale essenzialmente della teoria dell’affidabilità delle macchine e di diagrammi che descrivono i predetti scenari di eventi indesiderati. La valutazione dei rischi dovrà fornire un quadro generale ed esauriente dell’entità dei rischi presenti e consentire una successiva fase decisionale sugli interventi da realizzare. Dovranno essere definiti i limiti di accettabilità e gli interventi di prevenzione e/o protezione necessari per ridurre i rischi non accettabili ed eventualmente valutare strategie migliorative.
Strategia per migliorare la gestione della sicurezza
Per migliorare la gestione della sicurezza in un impianto chimico è possibile seguire diverse strategie, a seconda della complessità e del grado di pericolosità di un processo. In generale è utile seguire alcuni aspetti:
Scelta dei componenti idonei alle sostanze impiegate nell’impianto: come è noto ci sono ambienti di lavoro molto più pericolosi di altri, come gli impianti nei quali sono presenti sostanze tossiche o corrosive. In questi casi è fondamentale, prima di tutto, che tubi, pompe e anche componenti “minori”, come i raccordi, siano realizzati con tecnologie e materiali in grado non solo di gestire al meglio i processi, ma anche di resistere a fuoriuscite di liquido o improvvisi innalzamenti di temperatura dovuti a malfunzionamento.
- Corretta etichettatura: l’etichettatura delle sostanze chimiche è indispensabile per la sicurezza perché le sostanze chimiche sono naturalmente portate a legarsi tra loro o agli elementi presenti nell’ambiente dando vita a reazioni chimiche che quando non sono controllate possono essere molto pericolose. Inoltre, ogni sostanza chimica pericolosa deve essere identificata con una specie di carta d’identità, la scheda di sicurezza (SDS), che fornisce tutte le informazioni necessarie per trattare in modo adeguato il prodotto.
- Segnaletica efficiente: per garantire la sicurezza nei luoghi di lavoro è fondamentale anche la segnaletica, che serve per indicare le vie di fuga e i dispositivi utili in caso di emergenza, come gli estintori, ma anche per identificare senza possibilità d’errore le sostanze pericolose all’interno degli impianti. Alcuni cartelli sono necessari in ogni luogo, altri sono davvero specifici e sono destinati a esigenze particolari. Per rendere più sicuri gli ambienti è importante anche evidenziare le vie di fuga perché siano fruibili in sicurezza anche quando manca la luce, o c’è molto fumo. A questo scopo è molto utile la segnaletica fotoluminescente da installare sui pavimenti: si tratta di indicazioni che si illuminano al buio e sono visibili anche quando il fumo che sale dal basso copre i segnali presenti sulle pareti.
- Valutare strategie per minimizzare il rischio: come ad esempio l’utilizzo di una catena di reazione che non utilizza materiali pericolosi (materie prime o catalizzatori) o che non produce intermedi o sottoprodotti pericolosi, utilizzo di diversi solventi, fluidi termovettori o refrigeranti per eliminare quelli che possono essere tossici o infiammabili, utilizzo di materiali con punti di infiammabilità più elevati, punti di ebollizione e altre proprietà che sono lontane dalle condizioni operative del processo.
- Sistemi di controllo e monitoraggio integrato: per garantire la sicurezza di un processo industriale è fondamentale monitorare tramite una rete di sensori di misura i principali parametri operativi (temperatura, pressione, concentrazione, ecc..) e un sistema informatico in grado di controllare il processo e segnalare eventuali situazioni di pericolo.
Una gestione integrata della sicurezza (vedi immagine) si ottiene attraverso software specifici per l’analisi e la documentazione dei principali aspetti della sicurezza e impatto ambientale di un processo industriale. La figura è un esempio di come può essere articolato un processo di gestione integrata della sicurezza in un impianto complesso e mostra come la funzionalità dell’impianto, la tutela dell’ambiente e la sicurezza dei lavoratori siano tre aspetti dello stesso obiettivo.
FONTI:
http://ing.univaq.it/
Dispense di sicurezza degli impianti industriali – Politecnico di Milano
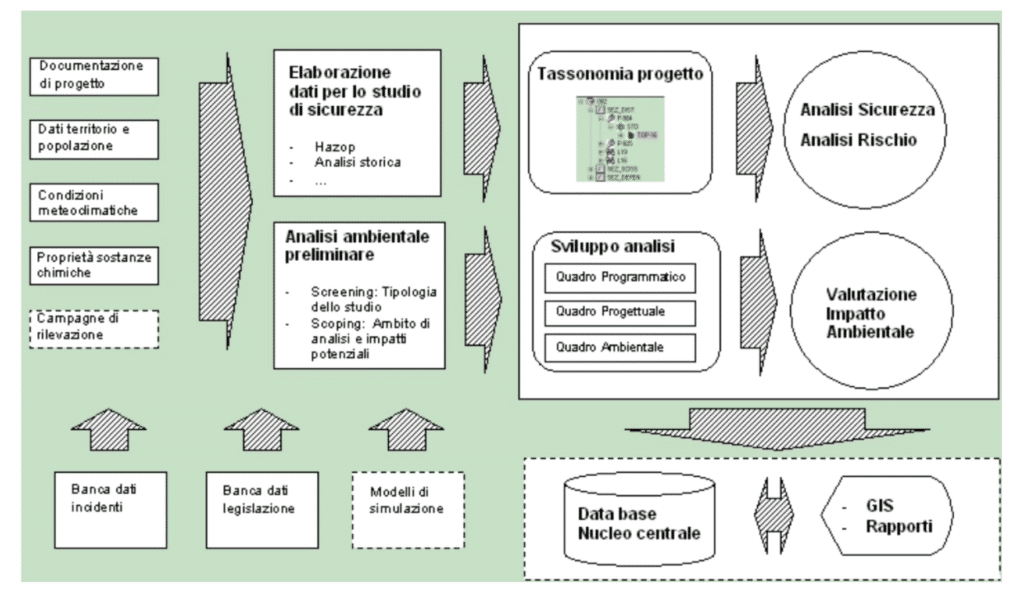
Lascia un commento