In ogni settore industriale, dal chimico-farmaceutico all’industria meccanica, dall’alimentare alla metallurgia e alla produzione di plastica e gomma, dalla produzione di energia all’industria galvanica, è di fondamentale importanza il controllo delle temperature; in questo articolo ci occuperemo della termoregolazione nell’industria galvanica.
Per ottenere prodotti e processi con standard elevati è essenziale riuscire a controllare la temperatura delle macchine, delle materie prime e dei fluidi in tutte le fasi di lavorazione. Questo è particolarmente importante in processi complessi come quelli galvanici.
Per garantire questo gli impianti industriali sono dotati di impianti di termoregolazione composti da due differenti circuiti: quello del fluido di lavoro e quello di servizio.
A seconda della temperatura che si vuole ottenere nel fluido di lavoro, il fluido di servizio può essere di diversi tipi come ad esempio:
- soluzioni antigelo, range di temperatura -30°C/ +90°C
- acqua, range di temperatura +5°C / +90°C
- olio diatermico, range di temperatura +30°C / +180°C
- olio siliconici e sintetici per applicazioni in un range di temperatura -100 °C / +260 °C;
- olio diatermico ad alta temperatura, range di temperatura +30°C / +350°C.
I due fluidi di lavoro si “incontreranno”, divisi da pareti solide, in uno scambiatore dove avverrà il trasferimento di potenza termica regolato dalle seguenti equazioni (In esse, i pedici c ed f si riferiscono rispettivamente ai fluidi caldo e freddo e i pedici e ed u all’entrata e all’uscita.):
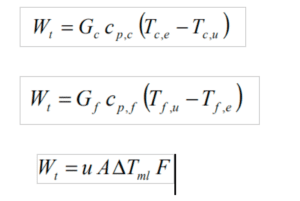
Dove:
W è la potenza termica
G è la portata massica
c è il calore specifico
A è l’area dello scambiatore
u è il coefficiente di scambio termico globale
F è un fattore di correzione che dipende dalla tipologia di scambiatore
la differenza di temperatura media logaritmica definita come:
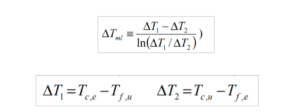
Appare quindi chiaro che la temperatura del fluido di lavoro che otterremo, oltre che dalla tipologia e geometria dello scambiatore, dipende anche dalle temperature, dai calori specifici e dalle portate dei due fluidi.
Per questo motivo, oltre allo scambiatore, altri due componenti essenziali di un circuito di termoregolazione sono le pompe e le valvole.
Le pompe, fornendo l’energia necessaria, permettono la movimentazione dei due fluidi, mentre le valvole regolano la portata e di conseguenza anche la temperatura finale del bagno termico. Lo stesso effetto si può ottenere installando una pompa a velocità variabile, che offre il vantaggio di non avere le perdite di carico introdotte dalle valvole.
La termoregolazione nell’industria galvanica
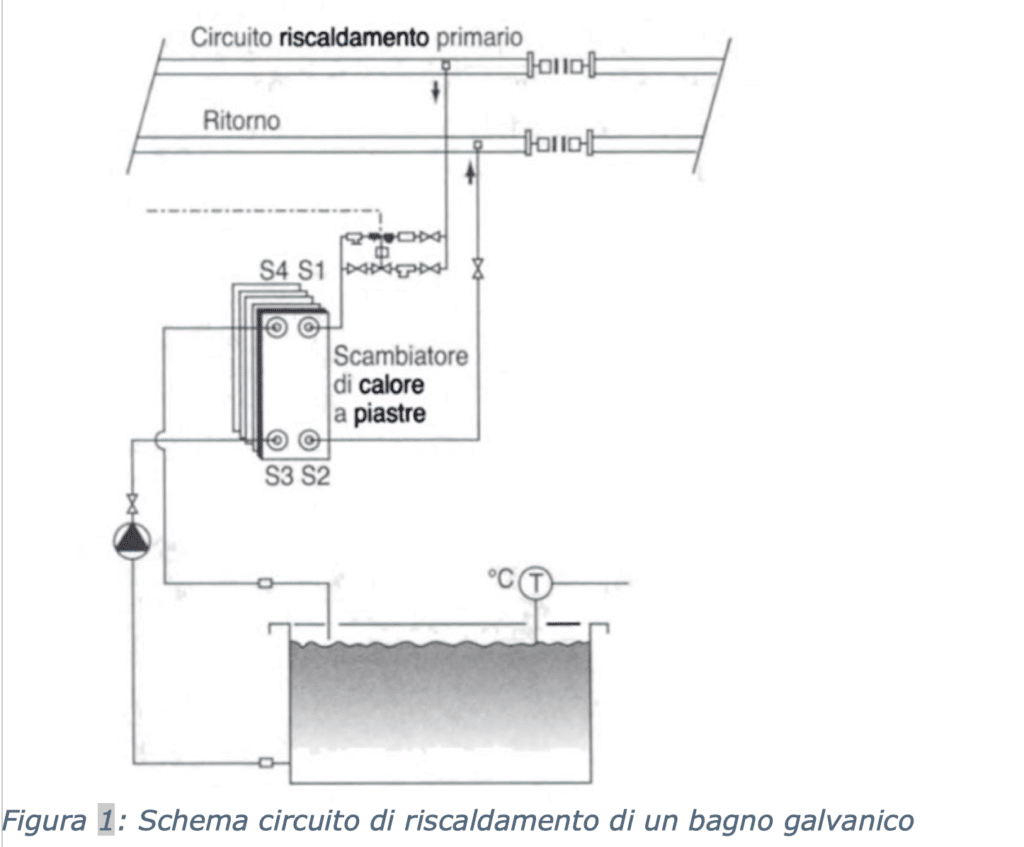
Nell’industria galvanica, gli impianti di termoregolazione vengono utilizzati per mantenere i bagni alla temperatura desiderata e permettere così il corretto deposito del trattamento superficiale sul prodotto da trattare.
I bagni galvanici sono altamente corrosivi: i bagni per il rivestimento con nichel sono costituiti da solvato di nichel, cloruro di nichel e acido bromico, quelli per la cromatura hanno come componenti acido cromico e solvato, mentre per i rivestimenti in lega di stagno e nichel vengono utilizzati bagni contenenti cloruro di nichel e di stagno, cloruro di ammonio, floruro alogenuro e acido cloridrico. Tutti i componenti che vengono a contatto con il fluido di lavoro devono perciò essere progettati per resistere ad ambienti altamente aggressivi.
Un esempio di pompa adatta a lavorare con questo genere di fluidi è la X-Class (https://www.asvstubbe.it/pompe-centrifughe/pompe-orizzontali/pompe-x-class/): questa pompa è molto resistente sia nella parte esterna, grazie alla scocca in metallo, sia all’interno, grazie alla possibilità di scegliere tra differenti rivestimenti plastici interni a seconda della tipologia e della temperatura del fluido da movimentare.
È nata proprio per applicazioni estreme e l’alta qualità di fabbricazione e il design innovativo garantiscono un’elevata durabilità anche a contatto con fluidi molto corrosivi.
Inoltre la tenuta meccanica sviluppata internamente, il particolare design della camera e la capacità di assorbire le vibrazioni garantiscono la sicurezza dei lavoratori anche in caso di perdite forti e improvvise.
Lascia un commento